Custom GB/T19001 1.5*3.3mm Hafnium Pellets
Place of Origin | Baoji, Shaanxi, China |
---|---|
Brand Name | Feiteng |
Certification | GB/T19001-2016 idt ISO9001:2015 GJB9001C-2017 |
Model Number | Hafnium Evaporation Pellets |
Minimum Order Quantity | To be negotiated |
Price | To be negotiated |
Packaging Details | Vacuum |
Delivery Time | To be negotiated |
Payment Terms | T/T |
Supply Ability | To be negotiated |
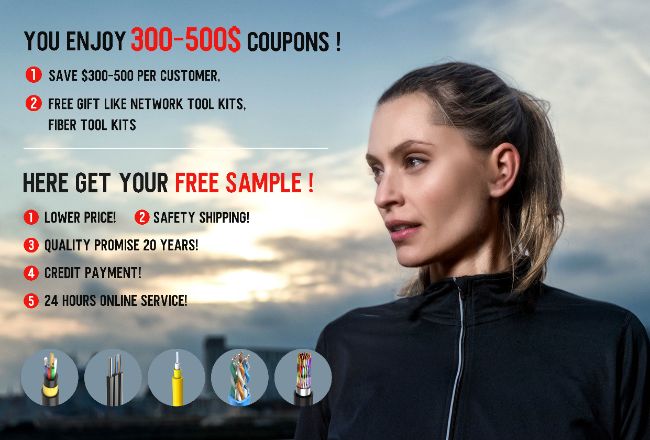
Contact me for free samples and coupons.
Whatsapp:0086 18588475571
Wechat: 0086 18588475571
Skype: sales10@aixton.com
If you have any concern, we provide 24-hour online help.
xCertification | GB/T19001-2016 Idt ISO9001:2015 GJB9001C-2017 | Port Of Delivery | Xi'an Port, Beijing Port, Shanghai Port, Guangzhou Port, Shenzhen Port |
---|---|---|---|
Packaging | Vacuum | Brand Name | Feiteng |
Size | φ1.5*3.3 | Material | Hafnium |
Place Of Orgin | Baoji, Shaanxi, China | ||
Highlight | 1.5*3.3mm Hafnium Pellets,GB T19001 Hafnium Pellets,Custom Hafnium granules |
Hafnium 1.5*3.3 Evaporation Pellets Packaging Vacuum
Port of delivery |
Xi'an port, Beijing port, Shanghai port, Guangzhou port, Shenzhen port |
Material | Hafnium |
Size | φ1.5*3.3 |
Packaging | Vacuum |
Vacuum coating is an important aspect of vacuum application field, it is based on vacuum technology, using physical or chemical methods, and the absorption of electron beam, molecular beam, ion beam, ion beam, radio frequency and magnetic control and a series of new technologies, for scientific research and practical production to provide a new film preparation process. Simply put, the method of vaporizing or sputtering a metal, alloy or compound in a vacuum so that it solidifies and deposits on the coated object (called a substrate, a substrate or a matrix) is called vacuum coating.
Advantages:
(1) Wide selection of film and matrix materials, film thickness can be controlled to prepare a variety of functional films with different functions.
(2) The film is prepared under vacuum conditions, the environment is clean, the film is not easy to be polluted, so the film with good density, high purity and uniform coating can be obtained.
(3) The bonding strength of the film and the matrix is good, and the film is firm.
(4) Dry coating does not produce waste liquid, and no environmental pollution.
Vacuum coating technology mainly includes vacuum evaporation plating, vacuum sputtering plating, vacuum ion plating, vacuum beam deposition, chemical vapor deposition and other methods. Except for CVD, the other methods have the following characteristics in common:
(1) all kinds of coating technology need a specific vacuum environment, in order to ensure that the film material in the process of heating evaporation or sputtering steam molecules formed by the movement, not by a large number of gas molecules in the atmosphere of the collision, block and interference, and eliminate the adverse effects of impurities in the atmosphere.
(2) A variety of coating technologies need to have an evaporation source or target, in order to evaporate the film material into a gas. Due to the continuous improvement of source or target, greatly expanded the selection of membrane materials, whether metal, metal alloy, intermetallic compound, ceramic or organic material, can be evaporated a variety of metal film and dielectric film, but also can be evaporated at the same time different materials to get multilayer film.
(3) evaporation or sputtering out of the film material, in the process of film generation with the workpiece to be plated, the film thickness can be more accurate measurement and control, so as to ensure the uniformity of the film thickness.
(4) Each film can be accurately controlled through the fine-tuning valve of the composition and mass fraction of the residual gas in the coating chamber, so as to prevent the oxidation of the evaporating material, reduce the mass fraction of oxygen to the minimum extent, but also can be filled with inert gas, which is not possible for wet coating.
(5) Due to the continuous improvement of coating equipment, the coating process can be continuous, thus greatly improving the output of products, and in the production process of environmental pollution.
(6) Due to the vacuum condition of the film, so the film of high purity, good compactness, bright surface does not need to be processed, which makes the mechanical and chemical properties of the film is better than electroplating film and chemical film.